機構設計者なら知っておきたい! 電子部品の発熱量計算と熱設計の基礎 第18回 [PICLS] 部品温度と放熱パターンの関係 (2)
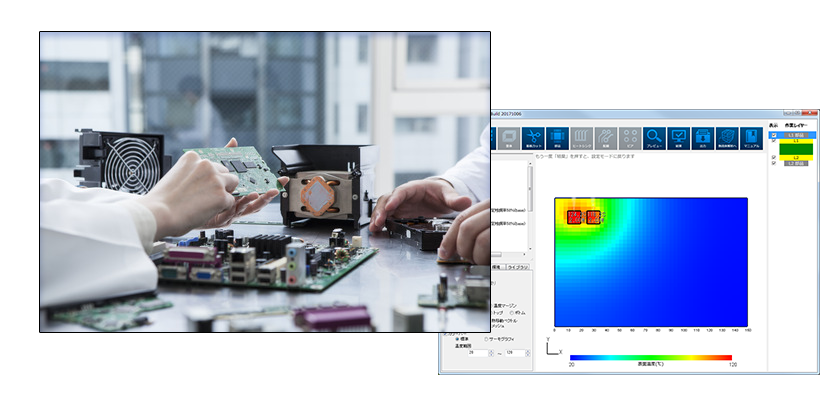
前回に引き続き、 PICLS で部品温度と放熱パターンの関係を見ていきます。
放熱パターンが薄い場合
前回は放熱パターンの面積に着目して部品温度を比較しましたが、今回は放熱パターンの銅箔厚との関係を見ていきたいと思います。部品は前回と同様ダイオードとし、発熱量は第15回で求めた値(0.371 W)、部品のサイズは7.6 mm × 4 mm × 2.8 mm とします。
では、PICLSを起動して設定を行っていきます。まず、① [寸法と構成] から基板を作成します。このとき、基板の大きさや層数は適当な値で構いませんが、L1の厚みを35 μm(デフォルト値)としてください。続いて、② [部品] をクリックします。ダイアログにダイオードの外形サイズと発熱量を入力し、基板の任意の場所に配置します。
次に放熱パターンを追加します。画面右上の作業レイヤーから ③ L1 をクリックします。そして、④ [配線] をクリックし、ダイオードの下にマウスドラッグで矩形の放熱パターンを配置します(大きさは適当で構いません)。⑤ 配置した配線部品をダブルクリックすると、配線(変更)ダイアログが表示されますので、[外形寸法] の [X] に [20][mm], [Y] に [10][mm] と入力し 適用 をクリックします。そして、マウスのドラッグ&ドロップで図18.1の位置に配置します。この状態で ⑥ [結果] をクリックすると、部品温度が図18.2のように表示されます。
図18.1 放熱パターンの配置
図18.2 放熱パターンの銅箔厚が35 μm のときの温度分布
放熱パターンの銅箔厚の影響
次に放熱パターンの銅箔厚を変更してみましょう。① [寸法と構成] をクリックし、L1の厚みを35 μm から70 μmに変更して、OK をクリックします。続けて、② [結果] をクリックして温度を確認します。結果を図18.3に示しますが、部品温度が低下していることが分かります。
図18.3 放熱パターンの厚みが70 μm のときの温度分布
このように温度が下がるのは、銅箔厚が増して、断面積が大きくなることによって、部品で発生した熱が逃げやすくなるためです。逆に銅箔の厚みが薄くなれば、熱抵抗が大きくなるため、その分部品温度は上昇します。
図18.4には部品温度と放熱パターンの面積の関係を銅箔厚ごとに示しています。厚みが増すほど放熱パターンの効果が大きく、また、面積を増やしたときの温度が下がり方も大きいことがわかります。
一方、銅箔の厚みが薄い場合には部品温度の下がり方が小さく、ある程度の面積に達すると、ほとんど冷却効果が見られないことがわかります。見逃されがちですが、この例のように、実装される基板が異なれば部品温度も大きく変わるということは極めて重要なポイントです。デバイスメーカーが提供しているアプリケーションノートには、放熱設計の例が記載されていることがあります。この場合、必ず想定している基板に関する記述がありますので、実際の基板と異なる箇所がないか確認することが重要といえます。
図18.4 部品温度と放熱パターンの銅箔厚の関係
次回からは、トランジスタについて説明します。
著者プロフィール
CrEAM(Cradle Engineers for Accelerating Manufacturing)
電子機器の熱問題をなくすために結成された3ピースユニット。 熱流体解析コンサルタントエンジニアとしての業務経験を生かし、 「熱設計・熱解析をもっと身近なものに。」を目標に活動中。
最後までお読みいただきありがとうございます。ご意見、ご要望などございましたら、下記にご入力ください