サクサ株式会社 様
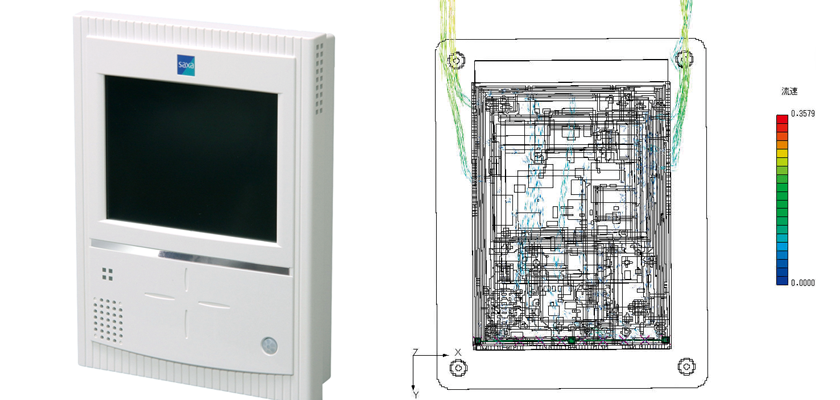
客観的に解析結果を評価できる環境の構築がカギ
電子機器向けの熱流体解析でよく使われる「熱設計PAC」を使って大きな成果を得ているのが、ビジネスホンや各種ネットワーク機器を手掛けるサクサだ。同社では熱設計のワーキンググループを発足させ、ソフトの検討やそれを活用するための社内ルールなどを作ったうえで、同ソフトを導入。1年で手戻りゼロなどを達成した。どのようにして熱解析ツールを使いこなすことができたのか、当事者たちに話を聞いた。
サクサは、ネットワークおよびセキュリティ関連ソリューションを開発、製造、販売する企業だ。2004年に田村電機製作所と大興電機製作所の経営統合によって設立された。オフィスで使われるビジネスホンや、カードリーダー/ライター、ホームセキュリティ機器など幅広く情報関連機器を取り扱う。
サクサが熱解析ツールを導入した背景には、CPUの高速化による発熱量の増加や、製品デザインの小型化、薄型化といった、設計環境を取り巻く変化があった。これらの急速な変化により、従来積み重ねてきた経験や勘だけで熱問題を予測することが困難になってきた。その一方で開発期間が短縮され、試作した後に放熱板や放熱孔を追加したり、設計への手戻りといった方法では間に合わなくなってきた。そこで、「実際にモノを作ってから直すのではなく、理論で裏付けられた熱設計」(サクサ 開発本部 機構開発部 技師の鈴木則明氏)の実践を目指すことになった。
サクサ 開発本部 機構開発部 技師 鈴木則明氏
そこでサクサは2008年に、熱解析ツールの導入と定着を目的とした、「熱解析ワーキンググループ」を発足させた。サクサには商品開発関連部門として、電気・回路設計を行うハードウェア開発部や、筐体全体を設計する機構開発部、またソフトウェア開発部などがある。熱に関する問題は従来、機構開発部が扱っていたため、ワーキンググループは同部のメンバー4名でスタートした。その後、熱問題を根本から解決するためには、ハードウェア開発部との協力が欠かせないことが分かり、同部の2名を加えて熱解析の課題に取り組んでいった。
精度と使いやすさで解析ツールを決定
ワーキンググループではまず、熱流体解析ツールの選定を行った。条件は、第1に解析精度が高く安定していること、そして第2に、同社には解析部門がなく設計者自身が解析しなければならないため、操作が簡単であることだった。まず、3社の熱流体解析ツールを選び、解析精度を確かめるため、自社の製品の解析を依頼した。その結果と実際の製品における各場所の温度を比較してみたところ、図1のようになった。X社では最大で実測値と126℃もの差があったが、熱設計PACは最大で22℃しかなく、精度の高さは抜きんでていた。またツールの操作性についても、あらかじめ設計した3次元CADデータを熱設計PACで読み込めば、そのまま変更作業どをせずにメッシュを切って解析できた。一方、他社のツールでは、メッシュ作成時にエラーが出て、その都度調整を行うなど非常に手間がかかったという。また解析する際のソフトウェアクレイドルのアドバイスも決め手の一つとなった。解析精度を高めるためのアドバイスが的確で、非常に信頼できるとの印象を持ったという。さらに、他社の解析ツールの使われ方を調べたりするなどさまざまな検証を行った結果、精度がずば抜けて高く操作が簡単で、しかも比較的廉価である熱設計PACに決定した。
図1 3社の熱解析ソフトの解析結果を比較した例
解析ツールを十分に活用できる環境を整備
解析ツールを導入してもうまく使いこなせず、定着しないというケースはよくある。そこでサクサは、解析ツールの運用ルールや、解析データの評価方法などを定め、着実に効果を得るための環境を整備した。
まずワーキンググループは、熱設計に関する手順書を作って社内に公開。さらに、製品ごとに熱解析が必要かをチェックするリストを作った。このチェックリストには熱問題が発生する可能性のある条件が並んでおり、一つでも該当するものがあれば熱解析を行うことになっている。「設計者が思い込みで熱設計は必要ないと判断してしまい、あとで問題とならないように、あらかじめ社内ルールを設けました」(鈴木氏)。これにより同社の多くの製品が解析の対象になるという。
そして重要なのが、解析する際の解析条件を記録するレポートのフォーマットを用意したことだ。これには部品の種類、それを実装する面、消費電力、サイズ、耐熱温度といった項目が並ぶ。部品の種類はCPUや無線IC、メモリ、レギュレータ、コイルなどになる。消費電力については実測値、推測値、最大値などの区別も明記しておく。たとえば消費電力にカタログなどに書いてある最大値を使ったのであれば、実測値に比べて信頼度が下がるため、解析結果が多少悪くてもこのまま次の工程に進めるといった判断を下すことができる。このように解析条件を正確に記述してあとに残すことで、出た解析結果の理由を冷静に議論できるようになる。また入力間違いや勘違いといったヒューマンエラーを防ぐのにも役立つ。ちなみにこれらの条件項目はハードウェア設計部門の協力がなければ設定できない。またこのレポートがあることで、ハードウェア開発と機構開発といった他部門との議論が可能になる。 また熱設計PACの操作については、独自の操作マニュアルを作成。ワーキンググループによる指導で勉強会も行った。今では機構開発部の21名全員が同ツールを活用しているという。通常は設計者の一部だけだったり、解析専任者が解析することが多い中で、これほどの浸透は珍しいと言えるが、マニュアルを見て数回ほど操作することで、きちんと身に付いたという。
設計の初期段階から熱解析を導入
サクサでは2009年9月に熱設計PACを導入した。事前のワーキンググループによる念入りな準備のかいがあって、活用はスムーズに始まったという。同社では同ツールを構想設計、詳細設計、量産設計の3段階で活用するよう定めている。「まず構想段階での解析が重要」(サクサ 開発本部 機構開発部 部長の原 耕一氏)だという。この段階ではハードウェアの条件はまだはっきり決まっていないが、おおまかな装置外形および内部の基板レイアウトを基に解析し、熱問題の起こりにくい形状の目安を立てる。それを設計条件としてハードウェア開発部に伝え、回路を設計してもらう。
>サクサ 開発本部 機構開発部 部長 原耕一氏
続いて詳細設計の段階では、回路設計および筐体設計データを取り込み、高い精度の解析を実施した上で、製品試作を行う。最後に量産金型を作るとともに最終的な解析を実施。そして量産試作を行い、実試験による熱データを得て、シミュレーションと比較する。実測値とずれていれば原因を確認し、次の解析にフィードバックして、ノウハウを蓄積し、精度の向上に役立てている。
図2はICカードを利用して個人認証を行う製品「カードターミナルCT-600」で、図3が同製品の熱解析を行った例だ。熱設計PACで対流が起きて放熱できるかチェックしながら、通風口の位置や数などを決定した。
(左)図2 サクサのICカードリーダー 「カードターミナルCT-600」
(右)図3 CT-600の熱解析を行った例
試作後の手戻りがゼロに
熱解析ツールを活用することによって、サクサではさまざまな効果が出ている。最も大きいのが、量産試作後の設計への手戻りがなくなったことだ。「今のところ解析精度が期待通りに出ているので、熱による問題は試作後には発生していません」(鈴木氏)。構想段階での解析によって、明らかにハード側で対策すべき問題をあらかじめ見つけて調整できるのも、おおいにプラスになっているという。以前は量産の時点で熱の問題が見つかり、断熱シートやヒートシンク、放熱シートといった部材を追加した上に、金型の改造費がかかってしまうといったことがあった。「この場合、金額面だけでなく、手戻りに伴う工数の増加もかなりのものになります。上流で解析することによって、こういった無駄な手戻りや費用がなくなるのです」(原氏)。
また熱解析ツールの導入は、部門間で協力して熱問題に取り組む上でプラスになった。熱問題は従来、機構開発部で対処してきたが、実際にはさまざまな要因が絡み合っている。ツールで解析することによって、高温になる原因と、その対処はどこですれば一番効率的かを論理的に示すことができる。熱解析ソフトを使うことによって説得力が増すとともに、熱解析の結果データがハードウェア設計とのコミュニケーションツールの役割も果たしているというわけだ。
積極的な取り組みとツールの使いやすさが成功のカギ
このように熱解析ツールがうまく定着した理由には、まずワーキングループがきちんと機能したことが挙げられるだろう。ワーキンググループのメンバーが日ごろ熱問題に向き合っていた本人たちだっただけに、根本的に解決しなければ将来さらに大変になることが予想でき、問題への取り組みも真剣だった。その結果、初期段階からの解析の実施や、客観的に解析結果を分析するための記録レポートなどといった仕組みが作られた。
また、ワーキンググループの取り組みを社内全体に報告する機会を持てたことも、成功の一因だったという。サクサでは同社の技術部門が集合して、日ごろの取り組みをアピールする「相模原フォーラム」というイベントがある。このフォーラムで、ワーキンググループは解析を実施する計画を発表した。その後、短期間で成功例を発表することができた。これによって、解析すれば問題を事前に解決できるということが社内に認知され、ますます活動しやすくなったのだという。
一方ツールの使い勝手の良さも、解析が根付いたポイントだということだ。解析を行うメンバーは設計がメインのため、熱流体に関する勉強の時間はあまり取れない。それでも熱設計PACは、設定さえ間違えなければメッシングおよび解析の時点でエラーなども起こらず、うまく使いこなせるという。設計業務の合間に行うだけに、エラーが頻繁に起これば使うのが面倒になってしまう。その点で熱設計PACはトラブルがなく、設計メンバーにとっても自然に受け入れることができた。
今後はさらに解析の設定値を見直して精度の向上を目指すという。また基本的な熱解析で高い成果が出たため、さらなる解析の応用も検討中である。サクサでは車載製品や屋外設置機器もあるため、雨水や日射に関する解析にも取り組んでみたいとのことだ。熱設計PACの上位バージョンであるソフトウェアクレイドルの汎用熱流体解析ソフト「STREAM」を検討しているという。
サクサでは使いやすく現場に合ったツールを選び、それを活用するための土台作りをしっかり行ったことで、短期間で成果を上げることができた。同社の取り組みは、同じように熱対策に悩む企業にとっておおいに参考となるだろう。
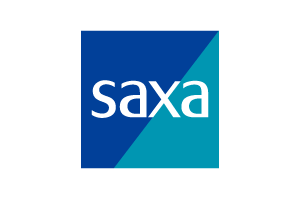
サクサ株式会社
- 設立:2004年4月1日
- 事業内容:ネットワークおよびセキュリティ関連ソリューションの開発、製造、販売
- 代表者:代表取締役社長:越川 雅生
- 東京本社:東京都港区
- 資本金:107億円(2011年3月31日現在)
※熱設計PAC、およびSTREAMは、日本における株式会社ソフトウェアクレイドルの登録商標です。
※その他、本インタビュー記事に記載されている会社名、製品・サービス名は、各社の商標または登録商標です。
※本インタビュー記事の内容は2011年1月現在のもので、予告なしに変更する場合があります。また、誤植または図、写真の誤りについて弊社は一切の責任を負いません。
PDFダウンロード